NEWS:
We will keep you informed. Current news about products, fairs and projects can be found here.
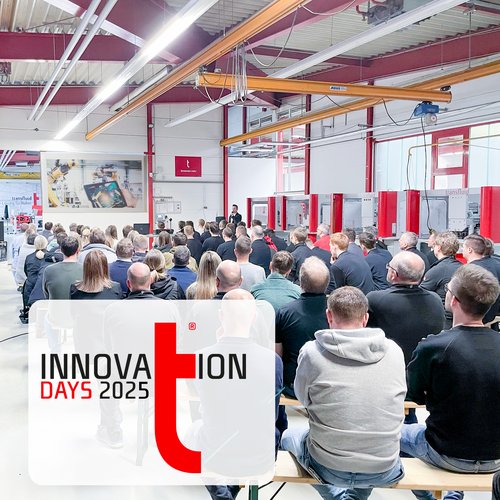
Innovation Days 2025
The industry meeting of the tube processing industry. Since 2006, transfluid has regularly brought together selected industry specialists for a joint…
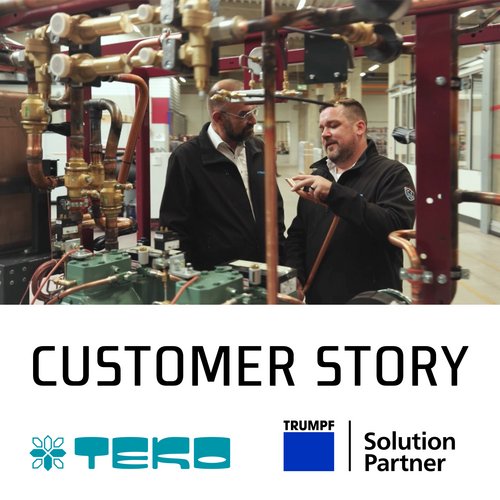
ALL GOOD THINGS COME IN THREES.
Highly flexible combination between laser tube cutting system and tube bending technology. Automated production of 12,000 different pipe geometries.
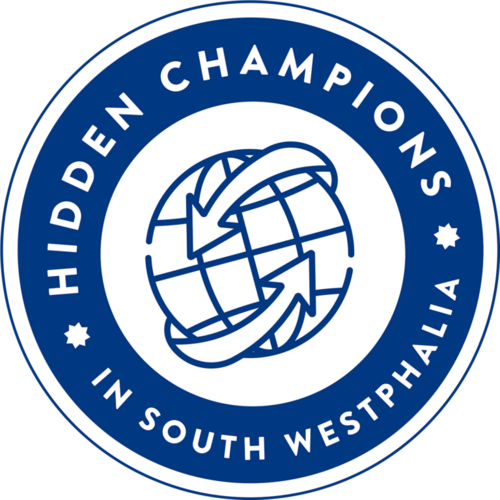
"Global market Leader"
Another award for the "global market leader from South Westphalia". The award is given to international companies that are technology leaders and…
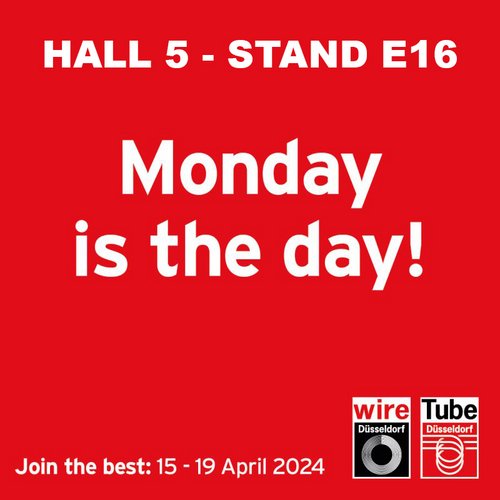
TUBE DÜSSELDORF 2024
The wire and Tube - Leading International Trade Fairs - opens its doors again next Monday and we can't wait to welcome you to the world's leading…
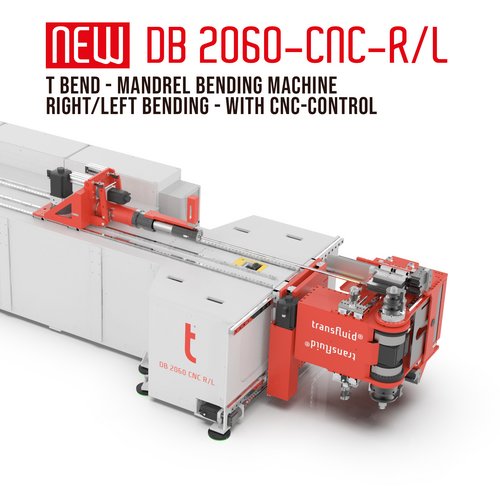
ABSOLUTE INNOVATION right/left bending up to ø 2 3/4"
With the new T bend CNC mandrel bending machines of the type DB 2060-CNC-R/L, steel, stainless steel and non-ferrous metal tubes can be bent as round…
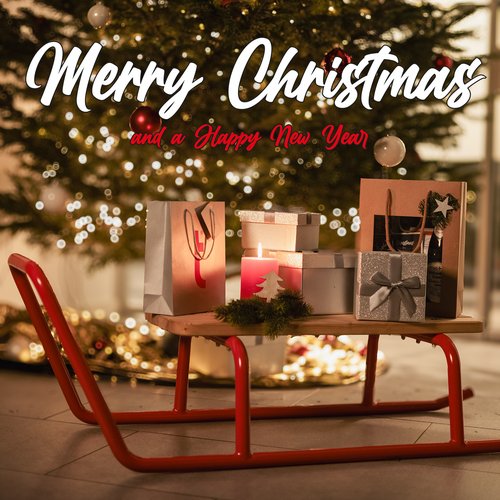
Merry Christmas
And a happy new year. The time before and around Christmas is a good opportunity to pause for a moment and remember all the good things you have…
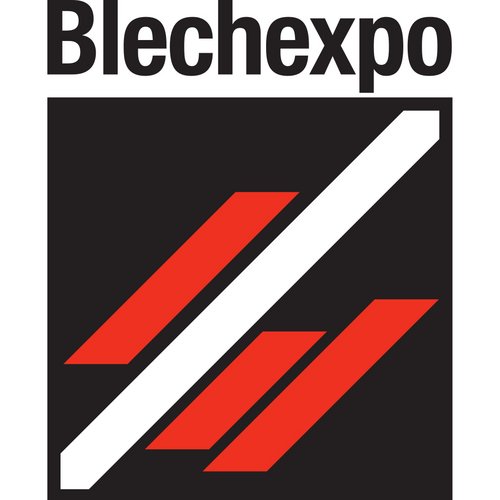
Meet us at the Blechexpo.
We will be attending Blechexpo Messe in Stuttgart again this year. From 07.11 to 10.11.2023 we will be in hall 3 at stand 3104 with our exhibition…
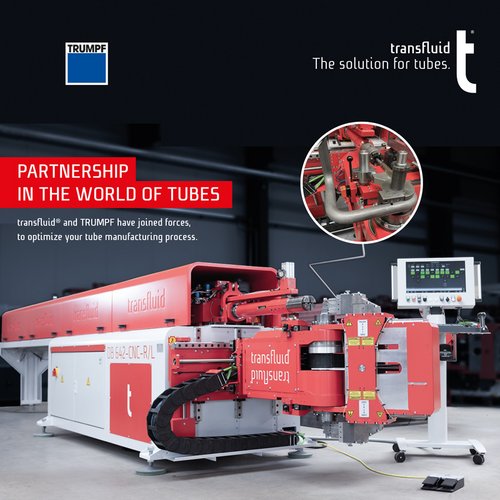
Partnership in the world of tubes
The partnership between TRUMPF and transfluid® enables highly flexible combinations between laser tube cutting systems and tube bending/forming…
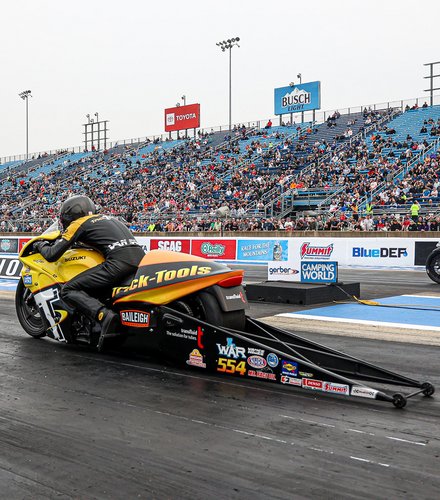
Get there fast with transfluid.
transfluid tube processing machinery Inc. becomes official sponsor of „Trick Tools Racing“ in the NHRA Pro Stock Motorcycle Series.
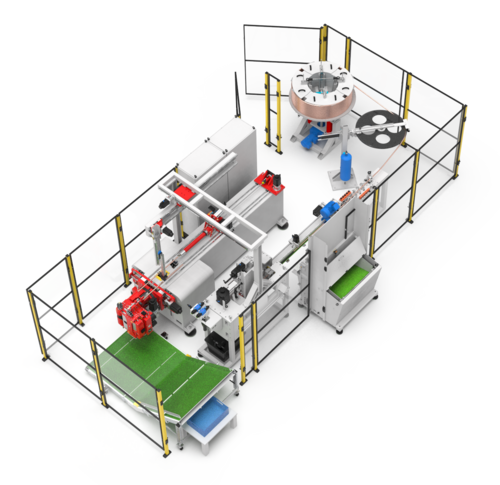
Compact manufacturing cell concept for fully automatic tube production
Due to the current demand in the field of renewable energies, especially with regard to heat pumps but also for domestic hot water systems, we have…
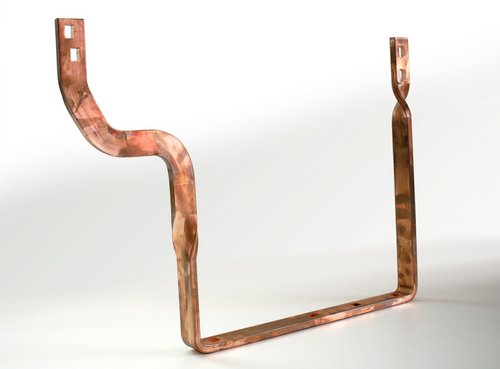
Busbars & Solid-material
Shaping the flow of energy. The bending machines from transfluid are known for their performance in tube bending, but they can also be used to bend…
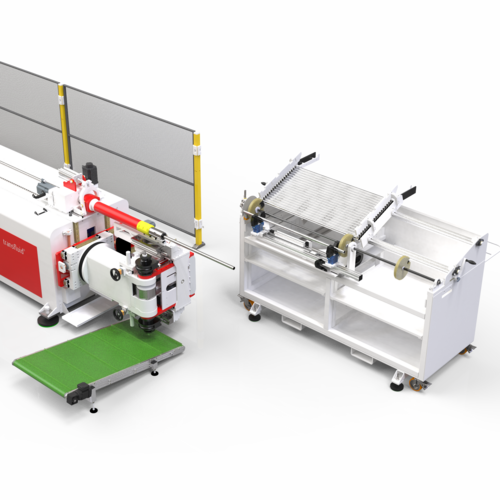
Cost efficient loading
To create even more flexibility especially for our cnc tube bending machines we designed an easy and less expensive loading unit.
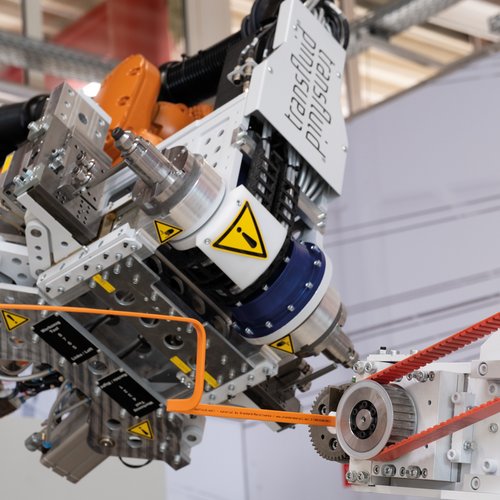
Shaping the flow of energy.
Extremely long busbars cut and bent automatically. Transfluid has developed a bending robot specially to meet the requirements for the production of…
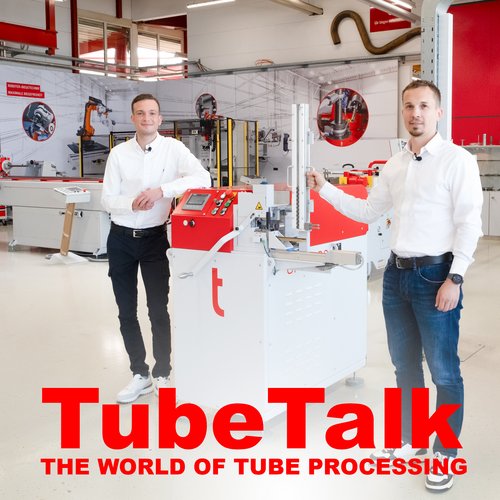
TubeTalk
We are pleased to invite you to our new series of videos explaining our products and production technology. 🎬