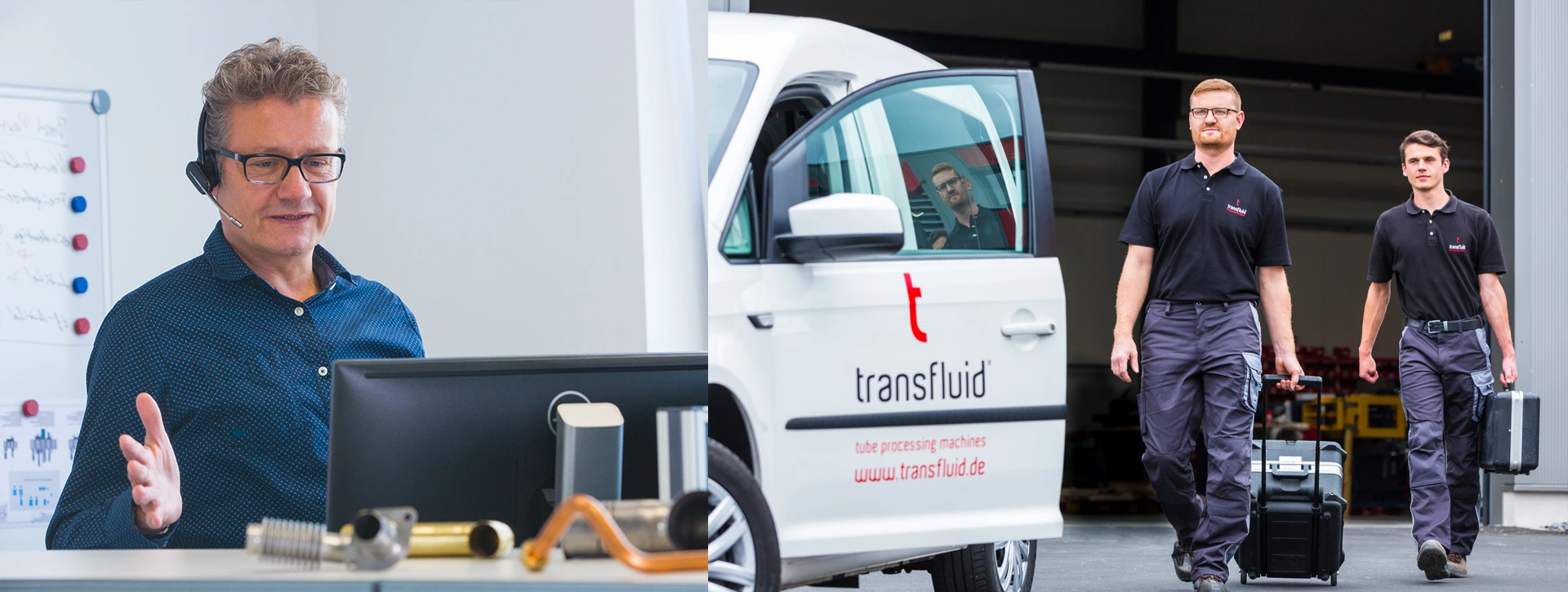
Our technical support
The strong 24-hour after-sales service from transfluid inc. also ensures the special sustainability of our solutions. Our service team are there for you. They will quickly provide you with an effective solution for optimised performance.
We offer you the right service options:
- Fixed service times, e.g. 24 hours after notification
- Specialised service and maintenance contracts for the preventive maintenance of your transfluid® machines and systems
- We are happy to support start-ups with feasibility tests so that the production of new products can start quickly and safely.
Your satisfaction is our benchmark!
The right machine for your task