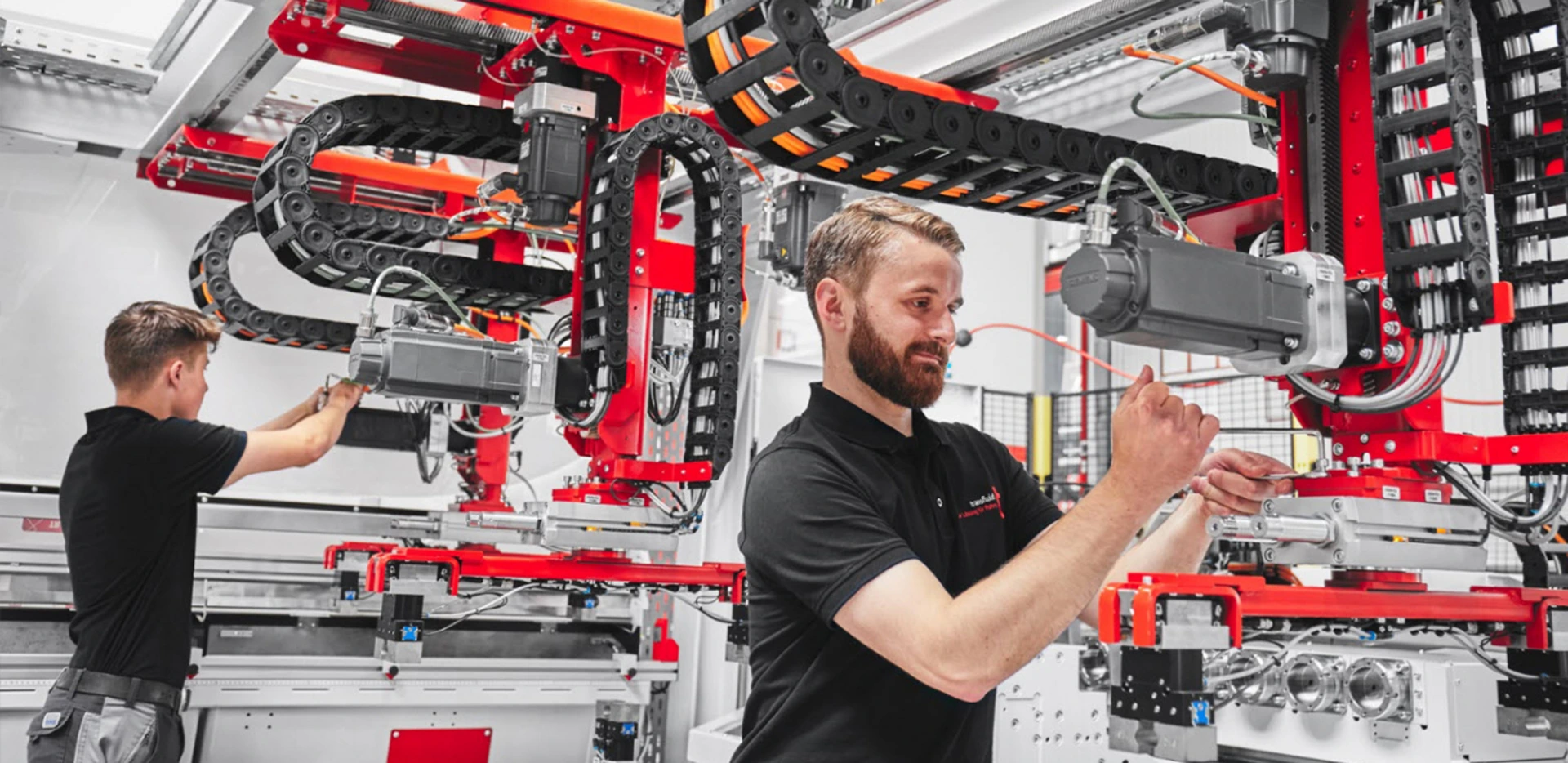
transfluid® PRECISE TUBE PROCESSING WITHOUT LIMITS.
The broad portfolio of transfluid machines offers solutions that are specific to your sector.
WE HAVE THE RIGHT SOLUTION.
With more than 30 years of experience and many projects completed successfully you will find a lot of know-how about tube processing in one place.
In our portfolio, alongside the valued standard solutions, there are highly efficient high-tech processes for small and large volumes. With the focus on flexibility and scalability.
-
AUTOMOTIVE
Mandrel bending & tube endforming machines.
Best solutions for the automotive sector.
See all -
HVACR
The specialist for tube bending and tube forming in the field of HVAC (heating, ventilation, air conditioning, refrigeration).
See all -
BUSBARS
Shaping the flow of energy.
See all -
HYDRAULICS
Forming variety and automatic bending for hydraulics.
See all -
SHIP BUILDING
Our effective tube processing with time and cost benefits.
See all -
FURNITURE INDUSTRY
Our tube processing brings your product in the best possible shape.
See all